Unplugged: Exploring Advanced Materials and Safety Standards in EV Charging Cables
- Vuong Loi Quang
- May 24, 2024
- 10 min read
Updated: Dec 5, 2024
High-voltage cables and connectors play a critical role in modern electrical systems, particularly in electric vehicles (EVs) and industrial applications. In this article, we will delve into the design considerations, innovations, and importance of these components in ensuring system performance and safety.
How do high-voltage cables differ from standard cables in design and construction?
High-voltage cables are designed and constructed differently from standard wires due to their specific purpose of transmitting high levels of electrical power. Here are some key ways in which high-voltage cables differ in their design and construction:

Insulation thickness: High-voltage cables require thicker insulation than standard cables. This is because higher voltages create greater electrical stress, which can lead to insulation breakdown. The thicker insulation helps prevent this breakdown and ensures safe power transmission.
Conductor size: High-voltage cables typically have larger conductor sizes than standard cables. This is necessary to accommodate the higher current levels associated with transmitting high voltages. The larger conductor size helps minimise power losses and maintain optimal efficiency in the transmission process.
Shielding: High voltage cables often have multiple layers of shielding to protect against electrical interference and external factors. These shields are typically made from metallic or non-metallic materials to provide a barrier that prevents the escape of electrical energy and minimises the impact of external electromagnetic fields.
Conductor material: High-voltage cables may use different conductor materials depending on the specific application. Standard options include copper, aluminium, or special alloys that withstand higher voltages and currents. The choice of conductor material depends on factors such as conductivity, mechanical strength, and corrosion resistance.
Impregnation or filling compounds: Some high-voltage cables are filled or impregnated with special compounds to enhance their insulating properties. These compounds can increase the cable's dielectric strength, improve thermal stability, and protect against moisture and other environmental factors that could impact performance.
Additional safety features: High voltage cables often incorporate other safety features such as voltage indicators or fault detection systems. These features help monitor the cable's condition, detect faults or abnormalities, and alert operators in case of potential issues.
It is important to note that high-voltage cables must adhere to strict regulations and standards to ensure their safe and reliable operation. Design and construction considerations are carefully implemented to meet these requirements and guarantee the efficient and secure transmission of high levels of electrical power.
What are some common types of HV connectors used in EV charging cables?
Several common types of High Voltage (HV) connectors are used in Electric Vehicle (EV) charging cables. These connectors are crucial in safely transferring power from the charging station to the EV's battery system. Here are some essential types of HV connectors commonly found in EV charging cables:
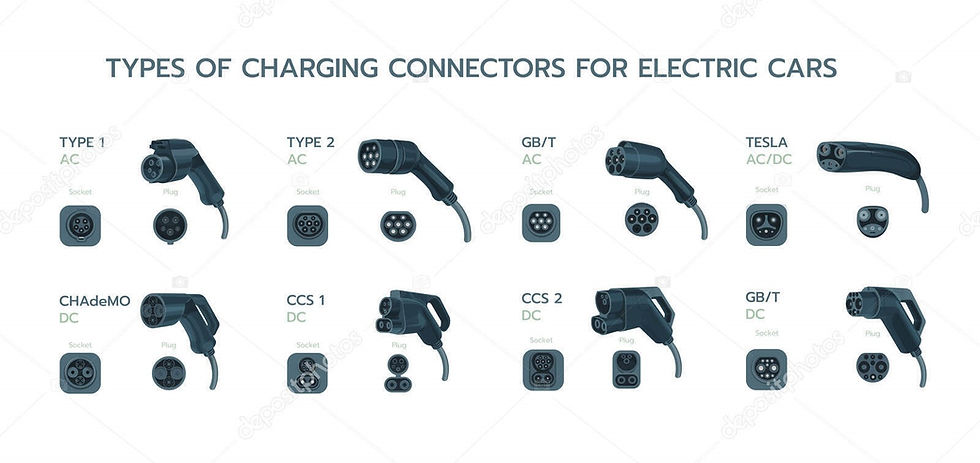
Type 1 (SAE J1772): This connector, also known as the SAE J1772, is widely used in North America and Japan. It features a J-shaped design with five pins and is mainly used for Level 1 and Level 2 charging. The Type 1 connector is compatible with most EVs produced in these regions.
Type 2 (IEC 62196-2): The Type 2 connector, also called the IEC 62196-2 or Mennekes connector, is commonly used in Europe. It has seven pins and supports both Level 2 and Level 3 charging. The Type 2 connector is compatible with most European EV models. CHAdeMO: This connector, designed by the CHAdeMO Association, is particularly prevalent among Japanese and Korean EV manufacturers. It features a unique “teardrop” shape and supports high-power DC fast charging. In some regions, CHAdeMO connectors are gradually being replaced by Combined Charging Systems (CCS).
Combined Charging System (CCS): The CCS connector, also known as the SAE J1772 Combo or IEC 62196-3, is widely adopted worldwide. It integrates the traditional Type 1 or Type 2 connector with two additional DC pins for high-power fast charging. CCS connectors offer both AC and DC charging capabilities.
Tesla Supercharger: Tesla vehicles have their proprietary charging connector, the Tesla Supercharger connector. This connector allows Tesla electric cars to access their dedicated Supercharger network for fast and convenient charging. Tesla Supercharger connectors are not compatible with other EVs.
Each type of HV connector has its specifications and compatibility, so it's crucial for EV owners, charging station operators, and manufacturers to ensure they use the appropriate connector for their specific requirements.
How does thermal management play a role in the design of high-voltage cables?
Thermal management plays a crucial role in the design of high-voltage cables. These cables carry substantial current and generate heat due to the conductor's resistance.
Temperature Control: Efficient thermal management ensures the cables operate within safe temperature limits, enhancing their overall performance and lifespan. Excessive heat can degrade insulation materials, leading to insulation breakdown and potential electrical failures.
Insulation Materials: Engineers employ various techniques for effective thermal management in high-voltage cables. One standard method is using thermal insulation materials with high thermal conductivity, such as mineral-based XLPE. This material helps dissipate heat efficiently, preventing temperature build-up.
Cooling Mechanisms: Another approach is to employ cooling mechanisms, such as circulating air or liquid cooling systems. Forced air cooling, where fans or blowers circulate air around the cable, can effectively reduce the operating temperature. On the other hand, liquid cooling involves the circulation of coolants through the cable to extract heat efficiently.
Heat Sinks: Additionally, cable designers may incorporate heat sinks or thermal conductive elements within the cable structure. These elements help dissipate heat and distribute it evenly, preventing hotspots that can compromise cable performance.
Layout and Environment: Furthermore, optimizing cable layout and considering environmental factors also contribute to effective thermal management. Placing high-voltage cables away from heat sources and ensuring proper ventilation can significantly enhance their cooling capabilities.
In conclusion, thermal management is a critical aspect of high-voltage cable design. By employing insulation materials with high thermal conductivity, incorporating cooling mechanisms, and considering layout and environmental factors, engineers can ensure that high-voltage cables operate within safe temperature limits, maximizing their performance and longevity.
What advanced materials are typically used in the construction of high-voltage cables?
A variety of advanced materials are commonly used in the construction of high-voltage cables. These materials are essential for safe and efficient electricity transmission over long distances. Let's take a closer look at some of the critical materials:

Insulation Materials: High voltage cables require insulation to prevent electrical current leakage. Advanced insulation materials, such as cross-linked polyethene (XLPE) or ethylene propylene rubber (EPR), are commonly used. These materials exhibit excellent electrical properties and high resistance to heat and environmental factors.
Conductor Materials: The conductor carries the electrical current through the cable. Copper and aluminium are the most commonly used conductor materials due to their excellent conductivity and mechanical strength. Copper is preferred for high-voltage applications due to its lower resistivity, but aluminium is often used in long transmission lines due to its lighter weight.
Shielding Materials: Shielding is necessary to protect the cable from external electrical interferences and to contain the electric field within the cable. Metallic shieldings, such as copper or aluminium tape or wire, are often applied around the insulation to provide an effective barrier against electromagnetic interference.
Jacketing Materials: The outer jacket of high-voltage cables provides mechanical protection and insulation from external environmental factors. Advanced materials like polyvinyl chloride (PVC), high-density polyethene (HDPE), or cross-linked polyethene (XLPE) are commonly used as jacketing materials. These materials offer excellent durability, weather resistance, and flame retardancy.
Filling and Damping Materials: Some high-voltage cables may require sealing or damping materials to reduce the formation of voids and vibrations. Epoxy resins or specialised gels fill the interstitial spaces between the conductor and insulation, providing mechanical stability and reducing the risk of electrical breakdown.
While these are some of the advanced materials commonly used in constructing high-voltage cables, it's important to note that the specific materials and their configuration can vary depending on the voltage level, application, and environmental considerations. Engineers carefully select and design the cable materials to ensure reliable and efficient electricity transmission.
What factors contribute to the durability of high-voltage cables?
High-voltage cables are designed to carry and transmit large amounts of electrical power over long distances. The durability of these cables is crucial for ensuring the safe and reliable transmission of electricity. Several factors contribute to the durability of high-voltage cables:
Insulation Material: The type and quality of insulation material used in high-voltage cables significantly affect their durability. Insulation materials such as cross-linked polyethene (XLPE), ethylene propylene rubber (EPR), or silicone rubber provide excellent electrical insulation and can withstand high operating temperatures. These materials are also resistant to moisture, chemicals, and UV radiation, enhancing the overall durability of the cables.
Conductor Material: The choice of conductor material is essential for the durability of high-voltage cables. Conductors of materials like copper or aluminium offer good electrical conductivity and are corrosion-resistant. The conductors should be able to handle high current loads without overheating or degrading over time.
Cable Design: High-voltage cables are optimised to withstand the stresses and strains they experience during operation. The wires typically comprise multiple layers, including a conductor, insulation, shielding, and protective sheathing. Each layer serves a specific purpose in enhancing the cable's durability and performance. To ensure long-term reliability, the design considers factors like temperature variations, mechanical stress, and potential electrical faults.
Installation Quality: Proper installation is crucial for the durability of high-voltage cables. Cables should be installed following industry standards and guidelines, considering factors such as proper bending radius, support structures, and protection against external forces. Professional installation ensures that the cables are not subjected to unnecessary stress, reducing the risk of damage or premature failure.
Maintenance and Monitoring: Regular maintenance and monitoring are essential for the longevity of high-voltage cables. Periodic inspections and testing, including thermal imaging, electrical measurements, and visual inspections, can identify potential issues before they become serious problems. Prompt repairs or replacements of damaged cables or components can prevent failures and extend the cables' lifespan.
Considering these factors, high-voltage cables can be designed, installed, and maintained to ensure their durability and reliable performance over their intended lifespan.
How does electrical stress impact the performance of high-voltage cables?
Electrical stress can significantly impact the performance of high-voltage cables. When high voltage is applied to a cable, it creates electrical stress within the cable insulation and conductor.
Partial Discharges: One significant impact of electrical stress is the formation of electrical discharges. These discharges, commonly known as partial discharges, can occur within or between the insulation and the cable's conductor.
Insulation Degradation: Partial discharges can degrade the insulation over time, leading to premature cable failure. This degradation's severity depends on the magnitude and duration of the electrical stress. Factors like voltage level, frequency, and impurities in the insulation material can also impact electrical stress.
Dielectric Strength: Additionally, electrical stress can cause the cable insulation to deteriorate and lose its dielectric strength. This can result in increased leakage current and decreased overall cable performance. When insulation is compromised, there is a higher risk of insulation breakdown and potential damage to the surrounding equipment.
Preventive Measures: Preventive measures can be taken to mitigate the impact of electrical stress on high-voltage cables. One approach is to design cables with appropriate insulation materials and thickness, considering the specific electrical stress levels they will be subjected to. Regular maintenance and monitoring of cable insulation integrity is also crucial to detect early signs of degradation or discharges.
In summary, electrical stress significantly affects the performance of high-voltage cables by causing insulation degradation, partial discharges, and potential breakdown. Considering the impact of electrical stress and implementing appropriate preventive measures is essential for ensuring the reliability and longevity of high-voltage cable systems.
What safety standards should be followed when designing and installing high-voltage cables?
When designing and installing high-voltage cables, following proper safety standards is paramount. These standards protect workers, the public, and the equipment itself. Here are some essential safety standards that should be followed:
NFPA 70E: The National Fire Protection Association (NFPA) 70E standard provides workplace electrical safety guidelines. It outlines safety measures to protect workers from electrical hazards while working with or near high-voltage cables. This standard emphasises using personal protective equipment (PPE), proper training, and safety procedures.
IEEE 1584: The Institute of Electrical and Electronics Engineers (IEEE) 1584 standard focuses on electrical arc flash hazard analysis. It provides methods for calculating the incident energy and arc flash boundaries. Adhering to this standard helps determine the appropriate PPE requirements and implement effective safety measures to prevent arc flash incidents.
NEC/CEC: The National Electrical Code (NEC) in the United States and Canada's Canadian Electrical Code (CEC) lay down the minimum safety requirements for electrical installations, including high-voltage cables. These codes cover various aspects such as cable sizing, insulation, grounding, and protection devices. Following the NEC or CEC ensures compliance with the legal requirements and promotes safe electrical installations.
IEC 60502: The International Electrotechnical Commission (IEC) 60502 standard provides specifications for power cables with rated voltages up to 30 kV. It covers design, construction, and testing requirements to ensure the safe operation of high-voltage cables. Adhering to this standard helps select the appropriate cable types and provides proper installation and performance.
OSHA Regulations: The Occupational Safety and Health Administration (OSHA) in the United States sets regulations and standards to ensure the safety and health of workers. These regulations include workplace electrical safety requirements, including those involving high-voltage cables. Compliance with OSHA regulations is essential to protect workers from electrical hazards, maintain a safe work environment, and avoid penalties.
When designing and installing high-voltage cables, it is vital to engage qualified professionals and experts who are well-versed in these safety standards. They can provide the necessary expertise and guidance to ensure compliance with the standards and promote a safe electrical environment.
What advancements have been made in cable design to improve safety and efficiency in high-voltage applications?
Advancements in cable design have contributed significantly to enhancing safety and efficiency in high-voltage applications. Let's delve into some key developments in this field:
Insulation Materials: The choice of insulation plays a critical role in high-voltage cable design. Modern cables utilise advanced insulation materials, such as cross-linked polyethene (XLPE), ethylene propylene rubber (EPR), or silicone rubber, which offer superior electrical and thermal properties. These highly breakdown-resistant materials can withstand extreme temperatures, ensuring reliable performance and increased safety.
Shielding Techniques: Shielding is essential to protect high-voltage cables from external electromagnetic interference and minimize the risk of electrical shocks. High-voltage cables now employ multiple layers of shielding, including metallic shields and semi-conductive layers. These shields effectively contain electric fields and prevent unwanted energy losses, improving overall efficiency and operational safety.
Surge Arresters: High-voltage applications are susceptible to voltage surges, which can cause damage to equipment and pose significant safety hazards. Modern cable designs incorporate surge arresters to mitigate the impact of voltage surges. These devices detect and divert excess voltage to the grounding system, safeguarding the cable and connected equipment from potential damage.
Fire Resistance: Fire can pose a severe threat to safety in high-voltage applications. Cable designers have significantly progressed in developing fire-resistant cables with enhanced flame-retardant properties. These cables are designed to withstand high temperatures and limit the spread of flames, ensuring the safety of personnel and minimising equipment damage in the event of a fire.
Diagnostic Capabilities: Monitoring the health and condition of high-voltage cables is crucial for ensuring their reliable operation. Advancements in cable design have introduced diagnostic features, such as embedded sensors and monitoring systems, capable of detecting faults, temperature variations, and insulation degradation. These diagnostic capabilities enable early identification of potential issues, facilitating timely maintenance and reducing downtime.
Cable Accessories: Developing innovative cable accessories has significantly improved safety and efficiency in high-voltage applications. Accessories like terminations and joints are designed to provide reliable electrical connections and insulation integrity, ensuring smooth power transmission and minimising the risk of failures or faults.
By leveraging these advancements in cable design, industry professionals can enhance safety levels and improve the efficiency of high-voltage applications, facilitating reliable power transmission and contributing to overall system reliability.
Conclusion
In conclusion, the design and innovation of high-voltage cables and connectors play a critical role in ensuring the efficiency and safety of high-voltage systems. By understanding the construction principles, design considerations, and the role of materials, we can optimize the performance and durability of these components. The continuous advancements and innovations in high-voltage connectors contribute to improved safety and efficiency.
Comentários